- Why Are Businesses Moving Toward Warehouse Automation?
- Final Thoughts: The Future Is Automated
- Frequently Asked Questions (FAQs)
Table of Contents
11 Benefits of an Automated Warehouse management System?
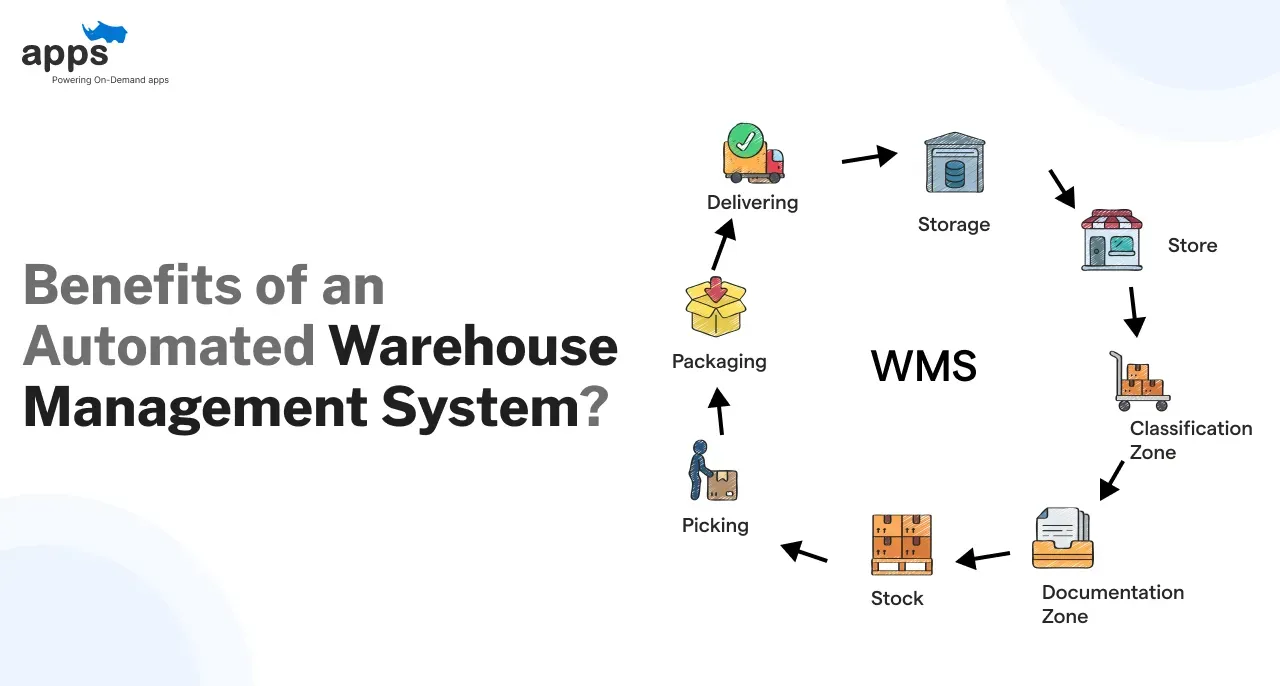
Managing a warehouse in 2025 means facing tighter margins, demanding customers, unpredictable staffing, and rising costs, often at once.
That’s why businesses are turning to Automated Warehouse Management. A Warehouse Management System (WMS) tracks your inventory, orders, and shipments, but it goes a step further when automated. From barcode scanners and robots to AI and real-time dashboards, automation is rewriting warehouses' operations.
The result? More speed & accuracy. Less chaos & bottlenecks.
The global automated warehouse management market is expected to reach $69 billion by 2025 (Statista).
It’s no wonder warehouse managers embrace warehouse management automation to stay competitive. From startups to eCommerce giants, the advantages of automated warehouse management system setups are hard to ignore.
Even for those looking to optimize space, automated warehouse inventory management helps deliver better performance with fewer resources.
Let’s see why.
Why Are Businesses Moving Toward Warehouse Automation?
The short answer? Because a manual just doesn’t cut it anymore.
With same-day delivery, global fulfillment, and shrinking margins, businesses need speed, precision, and control, and they need it now. That’s precisely where automated warehouse management starts making a measurable difference.
Here’s why warehouse management automation is skyrocketing
- Labor shortages are hitting hard.
- Customers expect real-time updates.
- Human errors = lost revenue.
- E-commerce is scaling faster than spreadsheets can handle.
In today’s landscape, relying on outdated systems isn’t an option. The advantages of automated warehouse management system adoption are clear: from streamlined processes to cost savings, it’s no longer a luxury but a necessity.
And the impact is visible. Whether inventory tracking or order fulfillment, automated warehouse inventory management improves visibility and accuracy while reducing manual labor.
In the words of Kardex,
“Automation isn’t just a convenience–it’s the only way forward.”
Let’s break down the 11 biggest benefits that automated warehouse management systems are bringing to warehouses today that automated systems are bringing to warehouses today.
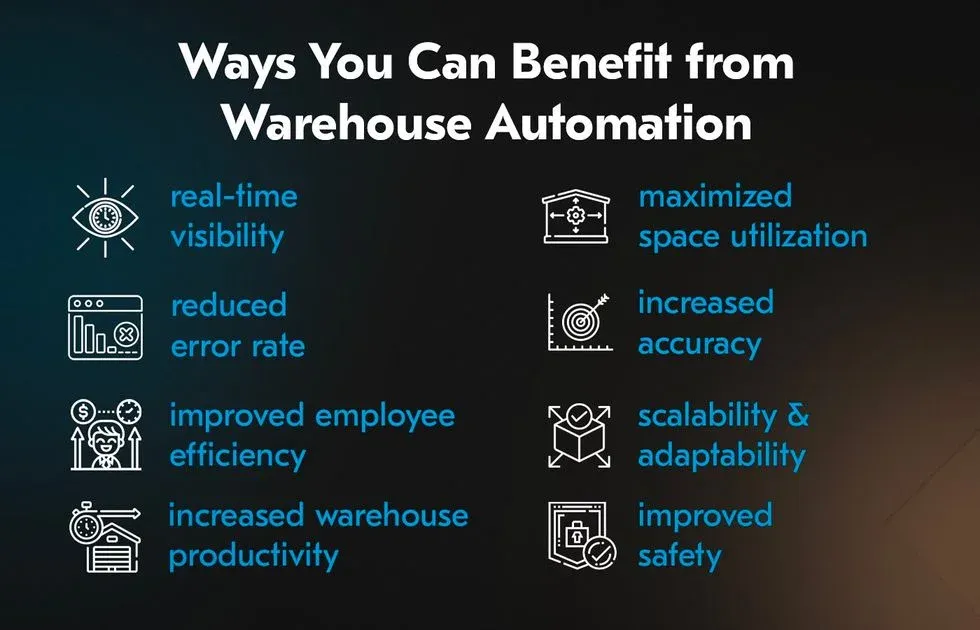
1. Near-Perfect Accuracy, Minimal Errors
Mistakes in warehousing aren’t just common, they’re costly. Whether mispicked items, misplaced inventory, or inaccurate counts, human error causes ripple effects throughout the supply chain.
However, with automated warehouse management systems, that risk is minimized dramatically.
Here’s how automated warehouse inventory management drives accuracy
- RFID tags and barcode scanners track every product's movement.
- Real-time updates ensure accurate inventory levels.
- System checks catch inconsistencies before they impact operations.
A notable example is Tesco, one of the UK's largest supermarket chains. After implementing RFID technology, Tesco improved its inventory accuracy from 65–75% to 93–99% (Source: Tagshopuk). This leap in precision ensures that orders are fulfilled correctly the first time, reducing costly returns and enhancing customer satisfaction.
Moreover, accurate inventory leads to better planning. When you know precisely what you have and where it is, forecasting, reordering, and restocking become more innovative and efficient.
Automation ensures compliance in regulated industries like pharma or food by maintaining detailed logs for every movement.
Bottom line: improved accuracy isn't just about avoiding mistakes. It's about creating a foundation for seamless operations.
2. Real-Time Inventory Visibility
Visibility is power. In a manual warehouse, information is often outdated before it’s even reviewed. However, automated warehouse management systems allow you to see and act in real-time.
Here’s what real-time inventory visibility means
- Live dashboards showing stock levels at a glance.
- Automated low-stock alerts and replenishment triggers.
- Instant updates across all locations and teams.
According to Meteor Space, only 9% of businesses have accurate end-to-end supply chain visibility. With warehouse management automation, that number can and should be much higher.
The advantages of automated warehouse management system setups extend far beyond speed and help ensure data reliability. Real-time visibility reduces errors, improves decision-making, and keeps teams aligned.
If a product is selling fast, the system flags it. If something is misplaced, you know immediately. And when customers ask about order status, your answers are based on up-to-the-minute facts.
Automation ensures transparency. And in logistics, transparency builds trust.
3. Faster Order Fulfillment
Speed isn’t a luxury anymore, it’s an expectation. Delays can cost you customers in the era of next-day (or even same-day) delivery. That’s where automated warehouse management systems shine.
Here’s how automated systems accelerate fulfillment
- Pick paths are optimized using real-time location data
- Robots handle repetitive transport without fatigue or delay
- Urgent orders are auto-prioritized in the system workflow.
Automated warehouse management makes the entire pick-pack-ship cycle faster and more reliable—no more waiting on manual sorting or hand-written packing slips.
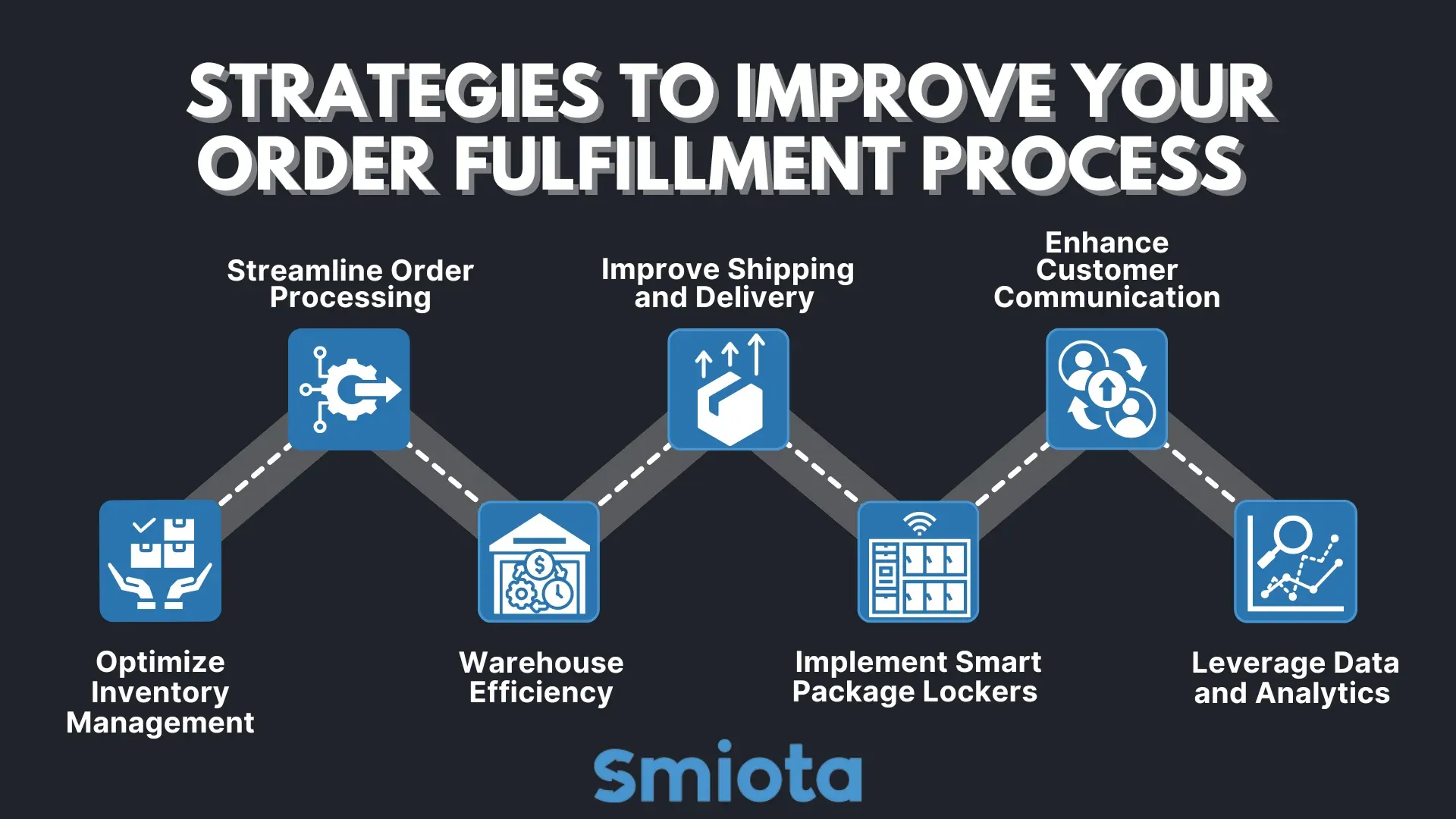
Consider the case of Deliverzen, a rapidly growing third-party logistics provider.
By implementing ShipHero's Warehouse Management System, Deliverzen scaled its operations from processing 3,000–4,000 orders daily to an impressive 7,000–8,000 orders. This transformation was achieved without increasing staff, highlighting the efficiency of automation.
And the advantages of an automated warehouse management system fulfillment don’t stop at internal gains.
Customers get what they ordered, when they expected it, every time. That builds trust, boosts loyalty, and minimizes costly customer service calls.
Speed isn’t about being flashy. It’s about being reliable, scalable, and competitive.
4. Smarter Space Utilization
Warehouse rent isn’t cheap. Every square foot not used effectively is money left on the table. That’s why automated warehouse inventory management is crucial in optimizing space.
Here’s how automation redefines layout efficiency
- Vertical lift modules tap into ceiling space, not just the floor
- Narrow aisles are usable since machines don’t need wide lanes
- Dynamic slotting software keeps high-turnover items within easy reach
Traditional setups often waste space due to static layouts and human limitations. But automation adapts in real time, reshuffling storage to maximise your footprint.
According to Kardex, implementing vertical and high-density storage solutions can recover up to 85% of floor space.
This significant space recovery allows businesses to store more inventory within the same footprint, delaying or eliminating the need for costly warehouse expansions.
Warehouse management automation allows you to delay expansion, reduce off-site storage, and improve flow without adding square footage. It also reduces clutter, which enhances safety and speeds up picking.
The advantages of automated warehouse management system layouts extend to energy efficiency and reduced walking distances, impacting the bottom line.
Less space wasted. More output delivered. That’s the power of thoughtful layout planning through automation.
5. Enhanced Labor Productivity
Labor is one of the most significant costs in warehousing and one of the hardest to scale reliably. While skilled workers are essential, a growing portion of manual labor is repetitive, physically demanding, and prone to error.
That’s where automated warehouse management gives your workforce a boost.
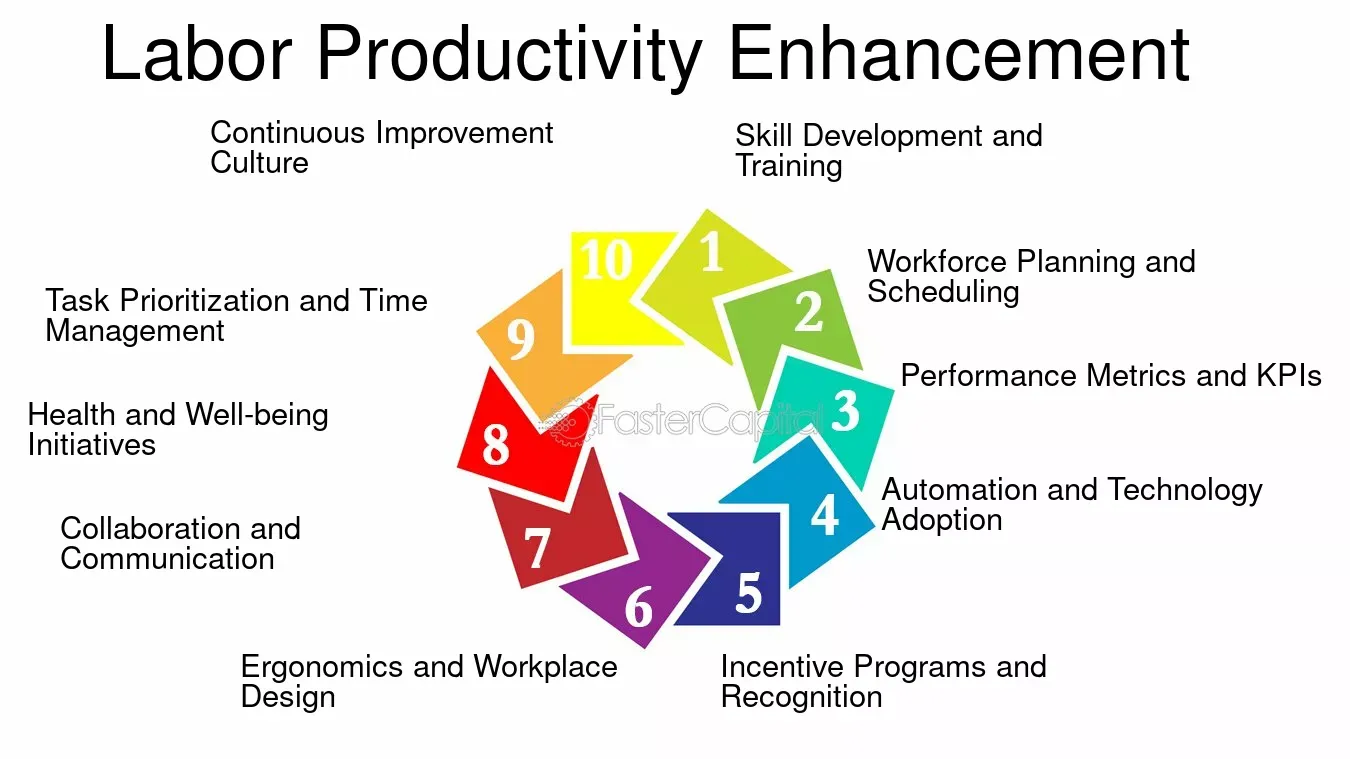
Here’s how automation enhances productivity:
- Robots and conveyors take over repetitive or physically intense tasks
- Workers shift focus to supervision, exception handling, or complex tasks
- Systems coordinate workflows to minimize downtime and walking distance
According to a report by McKinsey & Company, automation can improve warehouse labor productivity by up to 30%–50%, particularly in picking and sorting operations. This gain is about consistency, safety, and reducing burnout.
By deploying warehouse management automation, companies reduce reliance on temporary labor during seasonal peaks and gain greater control over shift planning. That’s critical in today’s tight labor market.
The advantages of automated warehouse management system labor optimization go beyond cost.
Happier workers, lower injury rates, and better retention are all downstream benefits. It’s not just a tech upgrade, it’s a workforce strategy.
6. Stronger Safety and Ergonomics
Warehouses are among the most injury-prone workplaces. Heavy lifting, repetitive movements, forklift traffic, and cluttered aisles contribute to sprains, strains, and even serious accidents.
However, many of these risks are drastically reduced with automated warehouse management.
Here’s how automation improves warehouse safety:
- Autonomous mobile robots (AMRs) move goods without human input
- Sensors and AI systems prevent collisions and flag hazards
- Vertical lift modules and goods-to-person systems reduce reaching, bending, and lifting
The U.S. Bureau of Labor Statistics reports that the warehousing industry experiences over 4.8 injuries per 100 full-time workers, many of which are preventable. By automating the riskiest parts of daily work, warehouses can dramatically reduce injury rates and associated costs.
Automated warehouse inventory management also keeps spaces more organized, reducing tripping hazards and creating safer workflows.
The advantages of automated warehouse management system ergonomics go beyond worker well-being. Safer environments mean fewer disruptions, fewer compensation claims, and a better reputation as an employer.
And with rising scrutiny on workplace safety standards, automation becomes more proactive.
Perfect choice. Seasonal scaling is distinct, high-impact, and not yet covered in your list.
7. Better Peak Season Management
Most warehouses can handle day-to-day operations just fine, but things can unravel quickly if they throw in a holiday sale or Black Friday rush. Delays, errors, and overworked staff. It’s the seasonal chaos retailers dread.
That’s where automated warehouse management gives your operation an edge.
Here’s how automation handles peak loads smoothly
- Robots and optimized workflows ramp up without needing more labor
- Orders are prioritized and fulfilled in real-time, not batched
- Intelligent analytics predict demand surges and auto-adjust inventory placement
A notable example is S.C. Manufacturing and Warehousing in North Finland. Facing significant challenges during their highly seasonal December operations, they implemented a purpose-built automation solution. (Source: Rocla AGV)
This strategic move streamlined their processes, ensuring operational reliability during peak periods.
By deploying warehouse management automation, you reduce your dependence on temp hires, overtime costs, and emergency shifts. Your systems scale with demand and have no stressor or any guesswork.
The advantages of automated warehouse management system scalability shine during seasonal peaks.
You maintain performance under pressure while keeping fulfillment costs predictable. And for your customers? It means gifts arrive on time, every time.
8. Data-Driven Forecasting and Inventory Planning
Running out of your best-seller or overstocking a slow mover can damage revenue and reputation. Forecasting is critical. Automated warehouse management makes it brighter.
Automation delivers a continuous stream of data: sales velocity, pick rates, inventory aging, and restock frequency. Layer in machine learning, and the system predicts what you’ll need before you know it yourself.
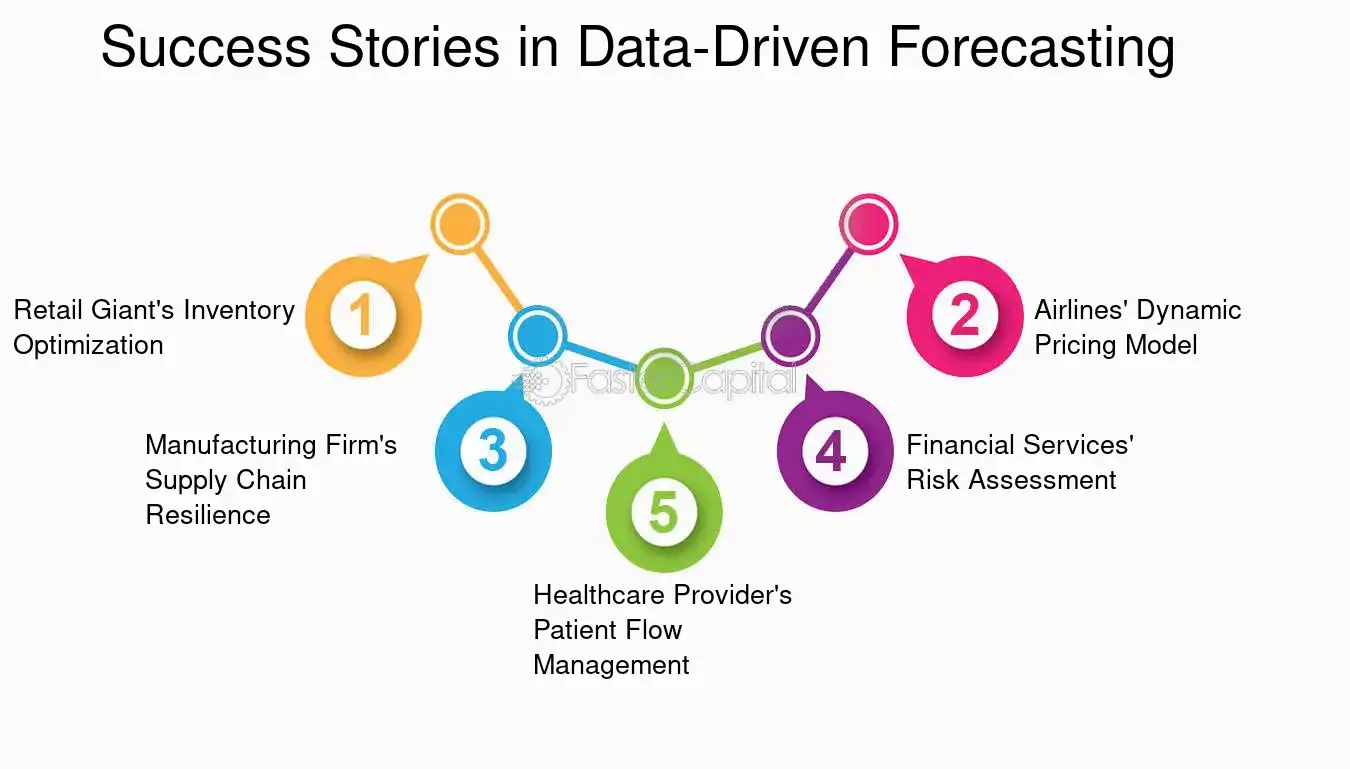
Here’s how it improves forecasting and planning:
- AI analyzes real-time and historical data to spot trends
- Reorder points adjust automatically based on demand signals
- Overstock, stockouts, and rush shipping costs are reduced
Deloitte emphasizes that predictive maintenance and analytics can empower supply chain systems to become “self-aware and self-regulating,” enabling smarter operational decisions across inventory planning, warehousing, and logistics. (Source: Deloitte Insights)
With automated warehouse inventory management, your planning goes from reactive to proactive. The system tells you what’s likely to happen next.
The advantages of an automated warehouse management system intelligence don’t end with inventory. You also gain insight into labor needs, equipment efficiency, and supplier performance. And that turns operations into strategy.
This kind of foresight is a massive competitive edge in a world where “just-in-case” stockpiling gives way to “just-in-time” precision.
9. 24/7 Operations and Consistent Reliability
Warehouses don’t sleep, but people need to. Shift schedules, staff fatigue, and unexpected absences limit manual operations.
Automated warehouse management solves that by delivering non-stop productivity.
Here’s what uninterrupted operations look like:
- Systems run continuously with no downtime between shifts
- Robots never call in sick or get tired
- Predictive maintenance detects and prevents breakdowns in advance
According to Vecna Robotics, automation facilitates 24/7 operations, enhancing productivity and meeting the increasing demands of e-commerce.
This doesn’t just impact output. Warehouse management automation improves service level agreements (SLAs), helps meet tight shipping windows, and enables businesses to offer faster, more reliable fulfillment.
The advantages of an automated warehouse management system ripple across the supply chain. Customers get what they want on time, systems self-correct before failures occur, and operations stay efficient, even in off-hours.
10. Improved Customer Satisfaction
It all comes back to the customer. Every item that arrives late, wrong, or damaged creates frustration—and possibly lost loyalty.
However, with automated warehouse management, accuracy and timeliness have become standard.
Here’s how automation supports customer happiness:
- Orders are picked, packed, and shipped with pinpoint precision
- Real-time tracking keeps customers informed
- Fewer returns and errors = fewer complaints
As highlighted by Cyzerg, automation boosts operational efficiency and significantly improves customer satisfaction by ensuring timely and accurate deliveries.
Warehouse management automation doesn’t just make back-end systems smarter. It delivers visible improvements to the front-end experience.
What are the advantages of an automated warehouse management system for customers? Faster service, better communication, and consistent quality turn first-time buyers into repeat customers.
11. Seamless Integration with the Supply Chain
A warehouse doesn’t exist in a vacuum. It’s one moving part in a larger machine. If your systems can’t connect with suppliers, transporters, and customers, you’re flying blind.
That’s why automated warehouse management is built to integrate.
Here’s how seamless integration improves coordination:
- Syncs with ERP, CRM, and shipping systems for real-time data sharing
- Auto-updates inventory when a supplier shipment or a return is received
- Tracks movement from the supplier dock to the customer door
According to Modula, integrating warehouse management systems with other enterprise applications optimizes picking and packing processes, maximizes resource utilization, and generates valuable data analytics.
With automated warehouse inventory management, all parts of your supply chain speak the same language. That means fewer miscommunications, better planning, and fewer customer headaches.
The advantages of automated warehouse management system integration aren’t just about tech—they’re about harmony across your operations.
Final Thoughts: The Future Is Automated
Warehouses have come a long way from pen-and-paper logs and manual stock checks. Today, the businesses that thrive adapt, automate, and evolve.
From faster shipping to fewer mistakes, from happier workers to scalable infrastructure, the benefits of automated warehouse management systems are too powerful to ignore.
And with logistics only growing more complex, now is the time to future-proof your operations.
AppsRhino and BotPenguin can help you start that journey. AppsRhino develops tailored warehouse automation and logistics apps, while BotPenguin brings AI-powered chatbots that streamline customer and warehouse communication.
Together, they create the infrastructure you need to scale smartly.
Don’t wait until your manual systems break under pressure. Choose automation. Choose control. Choose growth.
Reach out to AppsRhino and BotPenguin today and turn your warehouse into a powerhouse.
Frequently Asked Questions (FAQs)
What is AGV in warehouse management?
Automated Guided Vehicles (AGVs) are robotic systems used in automated warehouse management to transport goods.
They follow fixed paths, improving speed and consistency in warehouse operations with minimal human involvement.
What are the three levels of warehouse automation?
The three levels of automated warehouse management are basic mechanization (conveyors), semi-automation (AGVs, pick-to-light), and full automation (WMS + robotics).
Each level boosts productivity, accuracy, and operational scale.
How do AGVs and AMRs differ in warehouse automation?
AGVs follow fixed routes using wires or tracks, while AMRs navigate dynamically using sensors.
Both support automated warehouse inventory management, but AMRs offer greater flexibility in evolving warehouse layouts.
Can small businesses benefit from warehouse automation, or is it only for enterprises?
Absolutely. Scalable solutions in automated warehouse management let small businesses reduce errors, fulfill orders faster, and compete effectively.
Even modest automated warehouse management improves ROI and staff efficiency in growing operations.
What are the most cost-effective tools for starting automated warehouse inventory management?
Barcode scanning systems, mobile WMS, and smart shelving are affordable entry tools.
These provide key advantages of automated warehouse management system adoption—fewer errors, real-time tracking, and faster cycle counts.
How does predictive analytics improve warehouse performance beyond inventory forecasting?
Predictive analytics in WMS in logistics can optimize labor scheduling, anticipate equipment failures, and prevent order bottlenecks.
It adds intelligence to warehouse management automation beyond just managing inventory or demand
Table of Contents
- Why Are Businesses Moving Toward Warehouse Automation?
- Final Thoughts: The Future Is Automated
- Frequently Asked Questions (FAQs)